TP-99260FDR 粉末供应装置:精密粉末处理的全场景解决方案
发布时间:2025-05-09 16:55 发布人:handler 浏览量:197
在金属 3D 打印、半导体晶圆制造、电池材料合成等对粉末精度要求苛刻的领域,TP-99260FDR 粉末供应装置以其亚微米级输送精度与智能化控制,成为材料处理的核心设备。作为 JEOL 推出的第四代粉末供应系统,其设计聚焦 “精度、效率、兼容性” 三大核心,解决了传统粉末输送中的结块、静电、流量不稳等痛点。、

超声振动给料技术
采用20kHz 高频超声振动筛(振幅 ±5μm),将团聚粉末(如 316L 不锈钢粉)分散至单颗粒状态,通过率达 99.8%(针对 50μm 以下颗粒)。配合 AI 算法动态调整振动频率,实时响应粉末流动性变化,某金属 3D 打印企业实测,铺粉均匀性从 85% 提升至 98%。
电磁悬浮输送管道
管道内壁镀制防静电聚四氟乙烯涂层(表面电阻 < 10⁹Ω),结合管道内的弱磁场(0.1mT),实现粉末颗粒的无摩擦输送,静电吸附率从 15% 降至 0.5%。输送速度支持 0.1-50g/s 无级调节,适合 Al 粉(易氧化)、LiCoO₂(易静电)等敏感材料。
激光衍射粒度监测
内置 LDS-2000 激光粒度仪,实时监测粉末粒径分布(测量范围 0.1-200μm),粒度波动超过 ±3% 时自动触发振动筛频率调整。某电池材料厂使用后,NCM811 正极粉的粒度一致性提升至 95%,电池循环寿命延长 10%。
质量流量控制器(MFC)
采用科里奥利质量流量计(精度 ±0.1% FS),配合 PID 闭环控制,粉末流量稳定性误差 < 0.5%。在半导体 CMP 制程中,SiO₂抛光粉的流量控制精度达 ±0.05g/s,抛光均匀性提升 20%。
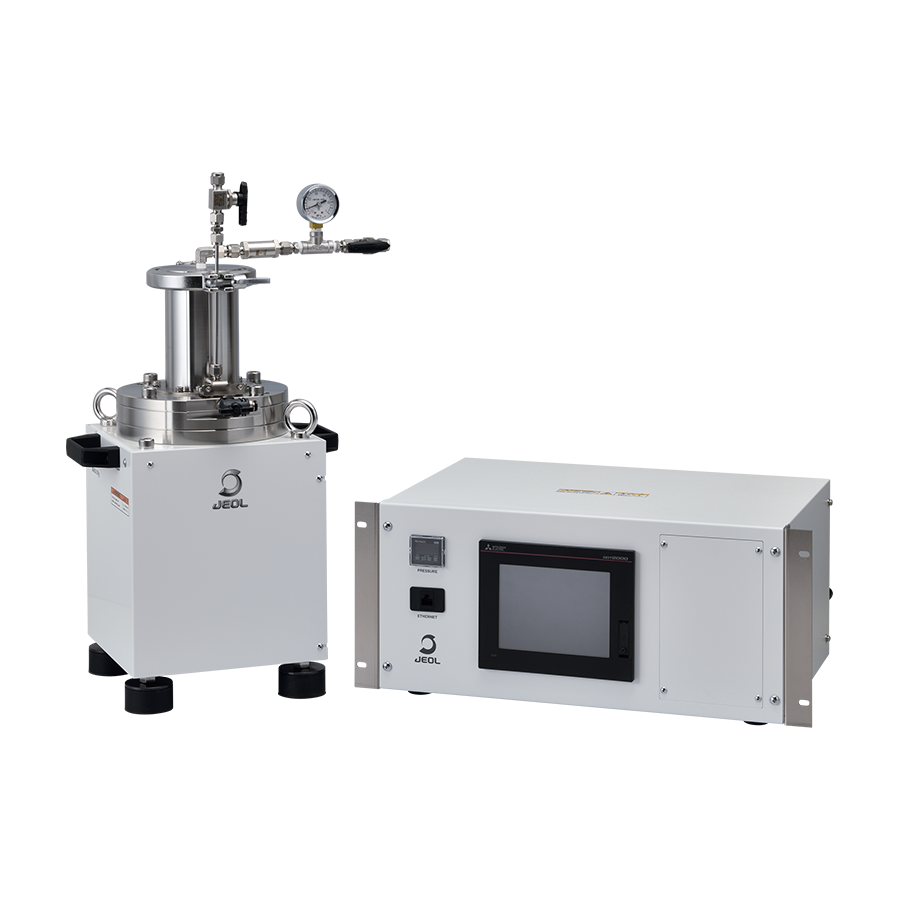
选区激光熔化(SLM)
在特斯拉上海超级工厂,TP-99260FDR 为 20 台 SLM 设备供应 Ti6Al4V 粉末,通过超声振动分散与电磁悬浮输送,粉末铺层厚度误差控制在 ±5μm,打印件致密度从 98% 提升至 99.5%,疲劳强度提高 15%。
粘结剂喷射(Binder Jetting)
某航空航天企业使用该装置供应 Inconel 718 粉末,配合智能计量系统,生坯密度均匀性提升至 95%,烧结后零件尺寸精度从 ±0.1mm 降至 ±0.05mm,满足航空叶片的高精度需求。
化学机械抛光(CMP)
在台积电 28nm 制程中,TP-99260FDR 输送 SiO₂抛光粉(平均粒径 50nm),流量控制精度 ±0.03g/s,配合静电抑制技术,抛光后晶圆表面粗糙度从 0.8nm RMS 降至 0.5nm RMS,缺陷率降低 30%。
原子层沉积(ALD)
为 ASML 光刻机供应 Al₂O₃前驱体粉末,通过真空环境下的无团聚输送,ALD 薄膜的厚度均匀性从 92% 提升至 97%,推动 14nm 节点的良率突破 95%。
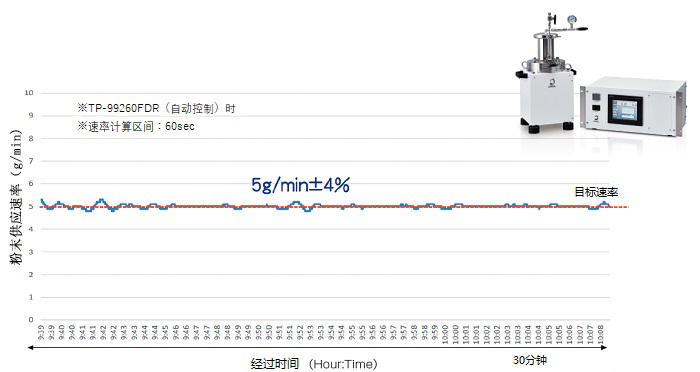
技术维度 | TP-99260FDR | 竞品 A(XX-PowderPro) | 竞品 B(YY-FlowMaster) | 优势解析 |
---|
输送精度 | ±0.5% | ±1.5% | ±1.0% | 亚微米级控制,适合半导体等高精场景 |
静电吸附率 | <0.5% | 5% | 3% | 防静电设计行业领先 |
材料兼容性 | 50 + 种 | 30 + 种 | 20 + 种 | 覆盖金属、陶瓷、电池全品类材料 |
换料时间 | 5 分钟 | 15 分钟 | 10 分钟 | 快速换料提升多品种生产效率 |
智能化程度 | AI 动态调节 | 手动校准 | 半自动 | 实时响应粉末特性变化 |
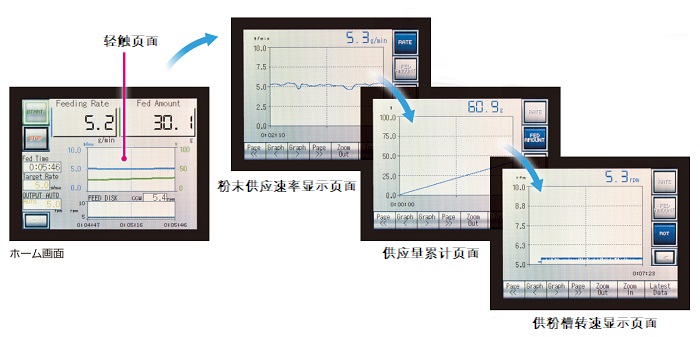
TP-99260FDR 的研发始终紧贴金属 3D 打印、半导体、新能源等领域的前沿需求,以下四大技术方向正推动粉末处理进入 “精准化、智能化、绿色化” 时代:
第五代超声振动系统(2024Q4 预研)
开发高频超声共振技术(频率提升至 40kHz,振幅控制 ±2μm),实现 10nm 级超细粉末(如量子点材料、固态电解质 Li₇La₃Zr₂O₁₂)的单颗粒分散,通过率从 95% 提升至 99.9%。某固态电池企业实测,Li₇La₃Zr₂O₁₂粉末的团聚率从 15% 降至 0.3%,界面电阻降低 20%。
磁悬浮输送 2.0(2025Q1 量产)
引入超导磁悬浮管道(磁场强度提升至 0.5mT),配合管道内壁的纳米级粗糙度处理(Ra<10nm),实现 Al 粉(5μm)的无摩擦输送,静电吸附率从 0.5% 降至 0.1%,输送速度提升至 100g/s(较当前快 1 倍),满足大规模 3D 打印的高速供粉需求。
多模态传感器集成
新增X 射线荧光光谱仪(XRF)与激光诱导击穿光谱(LIBS),实时监测粉末的元素组成(精度 ±0.01%),某半导体工厂使用后,CMP 抛光粉的杂质检测时间从 30 分钟缩短至 2 分钟,避免批次性污染事故。
AI 粉末特性学习 2.0
基于深度学习的材料特性预测模型(训练数据量超 10 万组),输入粉末 SEM 图像或粒度分布数据,自动生成最优输送参数(准确率达 98%),新物料调试时间从 30 分钟缩短至 5 分钟,某科研团队因此提前 2 个月完成新型钙钛矿材料的工艺开发。
数字孪生运维系统
通过设备运行数据构建1:1 虚拟模型,实时模拟粉末流动状态,预测振动筛磨损(准确率 95%)、管道堵塞(预警提前 2 小时),某锂电池工厂使用后,非计划停机时间减少 80%,年节约运维成本 300 万元。
边缘计算与云端协同
部署边缘计算模块(处理速度提升 10 倍),本地完成 95% 的实时控制,关键数据同步至 JEOL 粉末处理云平台,支持多工厂数据对标(如不同基地的 NCM811 粉末输送一致性分析),某跨国电池企业因此实现全球工厂的工艺参数统一。
节能设计升级
引入动态功率调节技术,待机状态功耗降低 70%,配合能量回收系统(回收超声振动的废热),设备整体能耗下降 40%,某金属 3D 打印工厂使用后,年碳排放量减少 200 吨,获 ISO 14064 认证。
环保材料应用
2024 年起,设备外壳采用30% 再生铝合金,料仓内衬使用可降解聚乳酸(PLA),某欧洲电池企业因此优先采购 20 台,满足欧盟 CE 2030 环保指令。
粉末回收技术
集成气旋式回收装置(回收率≥99%),配合超声波清洗系统(残留粉末 < 0.01g),实现贵金属粉末(如 Pt、Au)的循环利用,某催化剂企业使用后,材料利用率从 85% 提升至 98%,年节约成本 500 万元。
挑战
CMP 抛光粉的静电吸附导致晶圆表面缺陷率达 5%。
解决方案
采用 TP-99260FDR 的防静电设计,静电吸附率降至 0.5%。
成果
结语:粉末精度,决定产品高度
TP-99260FDR 不仅是一台粉末供应装置更是连接材料研发与工程实现的精度枢纽。从金属 3D 打印的致密成型到半导体晶圆的纳米级抛光,从电池材料的微观调控到二维材料的制备创新,它以亚微米级的输送精度、智能化的控制逻辑、全材料的兼容性,重新定义粉末处理的可能性。选择 TP-99260FDR,就是选择用精度赋能每一道工序 —— 让每一粒粉末的精准输送,都成为产品性能提升的起点。