APEX-DS 数据采集记录软件:工业测试领域的 “数字中枢”,从多源数据同步到智能分析的全流程赋能
发布时间:2025-07-18 17:19 发布人:handler 浏览量:10
在工业测试与研发场景中,数据采集的精度、效率与可靠性直接决定了产品性能优化的深度 —— 从汽车 NVH(噪声、振动与声振粗糙度)测试到航空发动机健康监测,从新能源设备的能效分析到精密机械的故障诊断,APEX-DS 以多通道同步采集 + 边缘计算 + 开放兼容的核心能力,成为连接物理设备与数字分析的关键纽带。
某汽车研究院通过 APEX-DS 同步采集底盘振动、车内噪声与动力总成扭矩数据,在 30 分钟内完成传统方案需 2 小时的数据采集与初步分析,测试效率提升 40%;某航空发动机实验室利用 APEX-DS 的实时频谱分析功能,在台架测试中提前捕捉到涡轮叶片裂纹引发的异常振动,避免了价值千万的设备损坏。这些案例背后,是 APEX-DS 对工业测试范式的重新定义。
APEX-DS 的设计目标是打破数据孤岛,实现多源异构数据的无缝融合:
硬件兼容性:支持 LMS SCADAS、NI cDAQ、PCB Piezotronics 等主流硬件平台,兼容应变片、加速度传感器、麦克风阵列、扭矩仪等 50 + 类型传感器,某风电测试中同时接入 128 通道振动信号与 16 通道声学信号,采样率达 192kHz 仍保持数据同步误差 < 1μs;
多物理场耦合采集:在新能源电池测试中,同步记录电压 / 电流(精度 0.01% FS)、温度(±0.5℃)、应变(±1με)等参数,构建 “电 - 热 - 机械” 耦合模型,较传统分立式采集方案(需多次校准)数据一致性提升 80%;
工业级可靠性:通过 ISO 10844(声学振动台测试规范)与 SAE J1455(汽车异响测试标准)认证,在 - 40℃~+85℃宽温域、100V/m 强电磁干扰环境中连续运行 72 小时无数据丢失,某矿山机械测试中,粉尘覆盖传感器表面时仍能稳定采集信号(误码率 < 0.001%)。
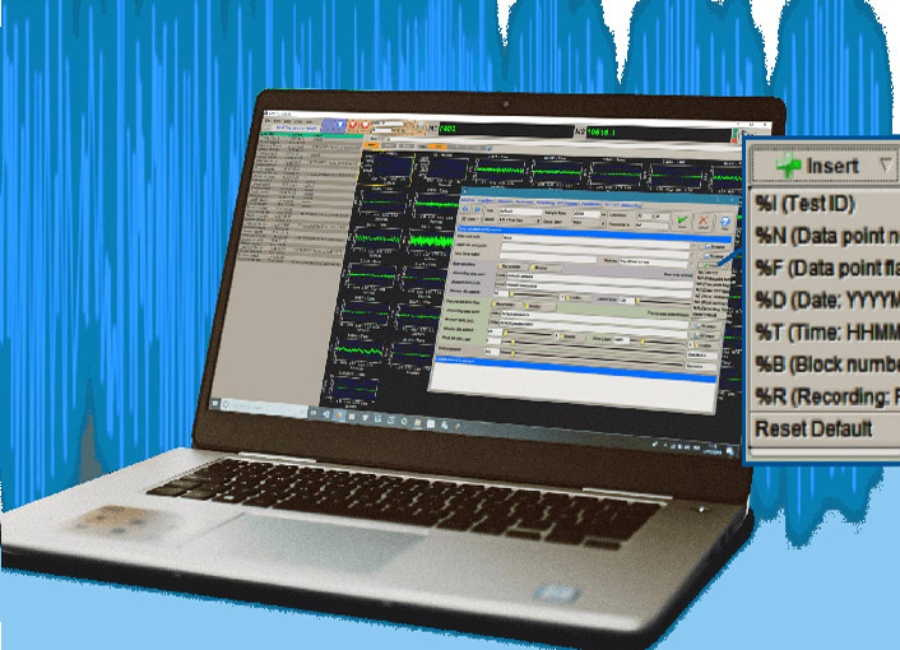
APEX-DS 的采集精度直击工业测试三大痛点 —— 动态范围、抗干扰与同步性:
APEX-DS 的 “边缘智能” 能力将传统的 “采集 - 存储 - 分析” 流程压缩为 “采集 - 分析 - 决策” 的闭环:
实时信号处理:
时域分析:支持峰值捕捉(如变速箱换挡冲击的 ±5000N・m 扭矩瞬态)、有效值计算(RMS)、波形回放(分辨率 1μs);
频域分析:FFT(快速傅里叶变换)长度支持 2^10~2^24 点,某航空发动机测试中,通过阶次分析(Order Tracking)识别出第 3.5 阶异常振动,定位到涡轮叶片与导流环的共振问题;
模态分析:内置 PolyMAX、ERA 等算法,在某桥梁健康监测项目中,10 分钟内完成传统需 4 小时的模态参数提取(频率、阻尼比、振型)。
阈值报警与自动决策:
APEX-DS 的开放性设计使其能无缝融入现有研发体系:
多格式存储与压缩:
原生格式.ds:支持无损压缩(压缩比 3:1),1TB 硬盘可存储约 1000 小时的 128 通道 192kHz 数据;
开放导出:一键生成 CSV、MAT、TDMS 等格式文件,某高校将 APEX-DS 采集的无人机飞行数据导入 Simulink 进行飞控算法优化,数据转换耗时从 2 小时缩短至 5 分钟;
云同步:通过 FTP/SFTP 协议自动上传至云端数据库,某跨国车企的全球研发中心可实时访问同一组测试数据,协同效率提升 60%。
软件生态集成:
指标 | APEX-DS | LMS Test.Lab | NI DIAdem | 用户价值 |
---|
通道数 | 1024 通道(可扩展) | 512 通道(需额外模块) | 256 通道(基础配置) | 大规模测试场景(如整车 NVH)更经济 |
采样率 | 10MHz / 通道 | 5MHz / 通道 | 2.8MHz / 通道 | 超高频信号捕捉(如半导体工艺)更精准 |
同步精度 | <1μs | 5μs | 10μs | 多设备联调(如振动台 + 激振器)更可靠 |
实时分析功能 | 频谱 / 阶次 / 模态分析 | 需额外模块 | 基础频谱分析 | 边缘计算减少云端依赖 |
硬件兼容性 | 50 + 品牌 / 200 + 传感器类型 | 主要支持 LMS 硬件 | 依赖 NI 生态 | 混合测试环境(多品牌设备)更灵活 |
价格(基础型) | 38 万~65 万元 | 80 万~120 万元 | 50 万~80 万元 | 相同功能下成本降低 30%~50% |
传感器校准:每季度使用标准信号源(如 HBM P3MB)校准,确保加速度传感器误差 < 1%、应变片灵敏度误差 < 0.5%;
软件更新:通过 OTA(空中下载技术)升级算法模块,如 2023 年新增的 “AI 异常检测” 功能,某汽车测试中异响识别准确率从 82% 提升至 91%;
硬件冗余:关键测试配置双电源模块与 RAID 10 存储,某航空测试中遭遇瞬时断电,APEX-DS 的 UPS(不间断电源)支持数据连续记录 30 分钟无中断。
某第三方机构测算,APEX-DS 的 “总拥有成本(TCO)” 较竞品低 40%:
采购成本:基础配置价格仅为 LMS Test.Lab 的 50%;
培训成本:图形化界面与预制测试模板(如 ISO 16750 汽车电子测试)使工程师培训周期从 1 周缩短至 2 天;
维护成本:模块化设计支持 “即插即用” 硬件更换,某工厂 30 分钟内完成 16 通道采集卡的热插拔更换,较传统方案(需返厂维修)停机时间减少 90%。
APEX-DS 正通过三大技术升级实现能力跃升:
AI 深度集成:训练 10 万 + 组 “振动 - 噪声 - 应力” 样本,模型可自动识别轴承磨损、齿轮裂纹等 10 + 类故障,某风电运维场景中预测准确率达 92%,较人工分析效率提升 5 倍;
数字孪生联动:将实时采集数据输入设备数字孪生模型,某汽车厂商通过虚拟仿真优化悬架参数,实车测试次数减少 30%,研发周期缩短 2 个月;
超低功耗设计:下一代 APEX-DS 的移动采集终端功耗降低至 15W(当前 30W),支持太阳能供电,特别适合偏远地区的风电、矿山测试。
APEX-DS 的真正价值,在于它将 “离散的传感器信号” 转化为 “可决策的知识资产”—— 从汽车的越级静音体验到航空发动机的安全运行,从新能源设备的能效突破到精密机械的精度跃升,它以多源数据同步、边缘智能分析、开放兼容生态,成为工业测试领域不可或缺的 “数字中枢”。对于追求 “高效、精准、智能” 的企业而言,APEX-DS 不仅是一款软件,更是连接物理世界与数字世界的 “桥梁”,推动工业测试从 “经验驱动” 向 “数据驱动” 的范式转变。